生産現場の技術継承・人手不足の問題をITの力で解決する、dynaEdgeソリューション。
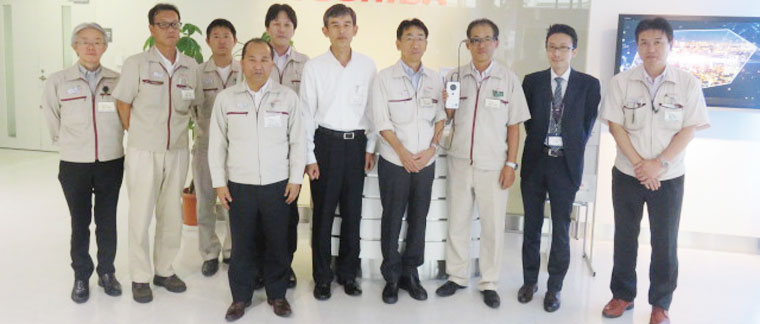
導入製品・サービス
モバイルエッジコンピューティングデバイス dynaEdge DE100/
インテリジェントビューア AR100/
作業支援アプリケーション Vision DE Suite
2017年7月、株式会社東芝の社内カンパニーから独立し、東芝グループの中で電子デバイス(半導体およびストレージプロダクツ)の研究開発、製造、販売を手がける東芝デバイス&ストレージ株式会社 様。
現在、多くの製造業において人材不足や技術継承の難しさなどが問題となっているが、それらは同社にとっても例外ではなく、喫緊の検討課題となっていた。そこで同社の姫路半導体工場ではモバイルエッジコンピューティングデバイスによる遠隔支援の導入を決定。ソリューションとしてdynaEdgeを選択し、さまざまな活用を模索するなかで根本的な解決を図ってきた。
今回はその中から、工場内のマシンキーパーによる活用例、および社外協力工場との連携における活用例の2つの活用例を紹介する。
-
-
東芝デバイス&ストレージ株式会社 様
2017年7月1日に株式会社東芝の社内カンパニーから事業継承により独立。ディスクリート半導体、システムLSI、HDD及び関連製品の開発・生産・販売事業、またその関連事業などを行う。資本金は100億円。年間売上高は、8,796億円 (連結) (17年度実績)。
工場内での活用例:課題と背景
人手不足およびベテラン社員から新人社員への技術継承が課題。
防塵服の脱着を要するため、建屋間の移動が時間のロスに。
美しい瀬戸内海に隣接し、昨年創設35周年を迎えた姫路半導体工場。約224,000m2という広大な敷地のなか、約1,300人 が小信号デバイス、パワーデバイス、ハイパワーデバイス等の半導体の製造に従事している。しかし、多くの製造業と同様、人手不足およびベテラン社員から新人社員への技術継承が課題となっていた。
同工場でトランジスタの製造を担う半導体製造第二部 第七トランジスタ課には生産に従事するオペレーター、装置の定期的なメンテナンスやトラブル発生時の対応を担うマシンキーパー等が所属するが、特にマシンキーパーの人材不足が顕著だった。当時の状況を第七トランジスタ課 主務の小田原 毅氏にお聞きした。
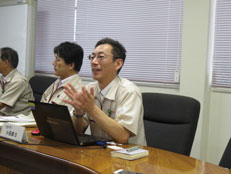
第七トランジスタ課 主務
小田原 毅氏
小田原氏「第七トランジスタ課に所属するマシンキーパーは、工場内にある3つの建屋に分散して配置されています。扱う製品が半導体ですから、作業中はクリーンルーム用の防塵服を着る必要があります。少人数で業務にあたるため、他の建屋に移動することもありますが、その際は防塵服の脱着と移動に20~30分の時間を要します。また、電話やメールでは十分な情報が得られず、必要な工具や治具を取りに再度自分の建屋へと戻ることもあり、人手不足に拍車をかけていました。さらに、交代勤務となっている関係から、時間帯によっては特定の装置に精通したスタッフがおらず、トラブルへの対応が難しいケースもあり、技術の継承、共有の面でも何らかの対策が必要とされていました」
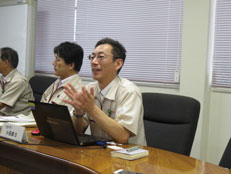
第七トランジスタ課 主務
小田原 毅氏
工場内での活用例:効果と展望
建屋間での連絡などに使用しマシンキーパーの人手不足を解消。
さらに動画つき作業マニュアルを制作して技術の継承を図る。
では、dynaEdgeの導入後はどう変わったのだろうか。
小田原氏「遠隔支援の実現により、現場と事務所、および建屋間での情報共有が進みました。例えばある装置でトラブルが起こり、その建屋のマシンキーパーでは対処できない場合、他の建屋のマシンキーパーに画面を見てもらい、アドバイスをもらうという活用をしています。また、ベテランのマシンキーパーにインテリジェントビューア AR100を着用してもらい、作業中の動画を保存。それをトラブルシューティング用のビデオマニュアルとして工程別に管理し、新人教育に活用しています。こうした動画を制作する場合、以前は撮影者や照明調整などが必要でしたが、dynaEdgeでは1人で完結でき、しかも自身で作業説明をしながら制作できるので、より早期に良質なものを制作することができるようになりました」
今後は活用範囲を他の生産拠点へと広げる計画もあると言う。
小田原氏「東芝グループ内には、他にも当工場と同じような装置を使っている工場があります。中には当社からマシンキーパーが出向しているところもありますが、限られた人材での対応にも限界があるため、今後はそうした拠点との接続も考えています」
dynaEdgeの活用により「通常は10年以上かかる」と言われるマシンキーパーの育成をどこまで短縮できるのか。今後も第七トランジスタ課の挑戦は続く。
社外協力工場との活用例:背景
姫路半導体工場と社外のアセンブリメーカーを接続。
実施にあたり接続回線の確保とセキュリティが障壁に。
姫路半導体工場ではdynaEdgeの社外での活用にも取り組んでいる。その内容について、技術部員として遠隔地でのトラブル解決および業務改善を担う技術部 参事の園部 浩徳氏にお話をお聞きした。
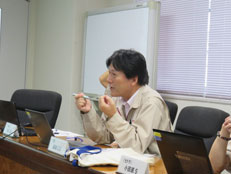
園部 浩徳氏
園部氏「当工場で生産したペレットの一部は、社外のアセンブリメーカーに送られ、単電子デバイスとして組み立てられます。そのなかから今回の工場を選定し、実証実験を行いました」
しかし、社外での使用開始にはさまざまな苦労が伴ったという。
園部氏「まずは接続回線の確保に手間取りました。当初はモバイルWi-Fiを購入し利用する事を考えていたのですが、工場内では遮蔽物が多く安定した接続が確保できませんでした。結局、十分にメリットを理解していただいたうえで、先方のLAN回線を利用させていただきました」
さらにセキュリティ上の問題もあった。
園部氏「協力会社とはいっても別会社ですから、制限なしに工場内の映像を配信することはできません。結局、先方の担当者が立ち会うという条件でdynaEdgeの利用が許可されました。また、社外からネットワークに接続するということで、当社側でもさまざまな許可が必要でした」
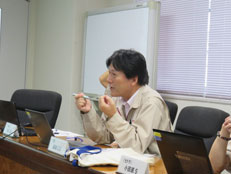
園部 浩徳氏
社外協力工場との活用例:効果と展望
遠隔支援で生産ラインの不良率のばらつき問題を即座に解決。
担当者の出張に比べ、2日間以上の短縮に。
現地スタッフのスキルアップにも期待。海外への導入を目指す。
そうした苦労の甲斐もあり、実際に大きな成果をあげた事例があったという。
園部氏「同一の生産工程で、装置により不良率が1%前後から11%前後までと大きく差が生じる事象が発生しました。そこで担当外スタッフにdynaEdgeを装着してもらい、こちらでオシロスコープの波形を確認したところ、不良率の高い装置に接続していたある部品に問題があることがすぐに確認できました。導入以前であればカメラ画像をメールで送ってもらい、口頭で指示をし、最悪の場合には工場から現地まで担当スタッフが出張して対応していたところです。今回のケースでは生産性向上まで2日間以上の短縮となったのではないでしょうか。不良率が高い間も生産を止めるわけにはいきませんから、その間のロスも考慮すれば導入効果はかなり大きかったと思います。また、遠隔による指示で作業する事によって、スキルアップが見込め、私達も複数の有識者で問題点の共有と的確な対策が出来るため、双方の技術レベル向上にも役立つ可能性があると考えています」
最後に、今後の展開についてお聞きした。
園部氏「現在は先方の立会いのもと遠隔支援を行っていますが、今後は利用ログを保存したり、配信画像を現地保存したりするなど、後から不適切な利用がなかったことを検証できる仕組みを作ることで、立会人不要で利用できる環境を整えたいと考えています。また、今回得た知見を活かし、タイのグループ会社などへの導入も目指したいですね」
国境を越えた遠隔支援ソリューションにより、技術者不足が解消される日も近いのかもしれない。
- BEFORE
- AFTER
- 装置の定期メンテやトラブル時の対応を担う
マシンキーパーの人材不足が顕著だった - ある建屋のマシンキーパーでは対処できない
事案でも精通したマシンキーパーから遠隔で
アドバイスを得て解決
- 交代勤務のため、特定の装置に精通した
スタッフが不在のこともあり、
技術の継承、共有の対策が求められていた - ベテランのマシンキーパーがAR100を着用、
作業中の動画を保存して
ビデオマニュアルに。新人教育に活用している
- 社外の協力会社の生産ラインで問題が
生じると、最悪の場合、現地まで
担当スタッフが出張することも - 現地の担当外スタッフにdynaEdgeを
装着してもらい、遠隔で検査機器のデータを
確認。その場で問題特定
BEFORE
- 修理技術の継承や現場作業員の
技術レベルUPが課題になっていた - 現場の技術者が電話で指示を受ける場合
両手で作業ができなかった - 1ヶ月あたり15日間も
本社技術者の出張が必要だった
AFTER
- 本社側から映像で現場の状況を把握
音声や画像で直接アドバイスできるように - 指示を受けながら両手作業が可能になり
作業時間が約半分に - 遠隔指示により
現場出張が約半分にまで減少
この事例で導入した製品・サービス
dynaEdge 関連製品の紹介
-
dynaEdge DE100は、蓄積したデータを、遠く離れたクラウドではなく、保守現場や工場ラインなどのエッジ側でリアルタイムに処理するモバイルエッジコンピューティングに対応。
インテル® Core™ m7-6Y75 vPro™ プロセッサー -
高品質な映像と音声によるコミュニケーション機能で生産性向上をサポート。快適な装着感と操作性でストレスのない作業環境を実現します。
-
Vision DE Suiteは、DE100とAR100専用に開発された作業支援アプリケーション。エキスパートが現場作業者を支援するためのさまざまな機能を提供します。
製品の導入・購入に関するご相談・お問い合わせ
※上記コメントはお客様の個人のご意見・ご感想であり、当社の見解を示すものではありません。
※製品、サービス、サポート内容は、弊社お問い合わせ窓口(Dynabook株式会社)までお問い合わせください。
製品の仕様・機能は予告なく変更する場合がありますので、ご了承ください。